Imagine shrinking an entire laboratory into a device the size of a business card
That's the essence of Allozymes' groundbreaking technology. By manipulating minuscule liquid droplets, we've revolutionized the way enzymes are discovered and engineered.
This shift from bulky, resource-intensive labs to compact, efficient microfluidic systems has far-reaching implications for sustainability.
Traditionally, enzyme research has been a wasteful process, generating mountains of plastic waste and hazardous byproducts.
Our microfluidic approach drastically reduces this environmental footprint by 600x.
By conducting experiments on a microscopic scale, we use significantly less plastic, water, and chemicals. It’s like transforming an ax into a fine scalpel – achieving the same goal with far less waste. This drastically reduces the reagents needed for testing down to microliters, and ultimately minimizes biohazard waste generation.
For instance, discovering a single ideal enzyme variant typically requires tens of thousands of experiments, producing up to 1,600 liters of biohazardous waste.
Our technology minimizes this by up to 99%, making enzyme research not just efficient but also environmentally responsible.
Learn more about our technology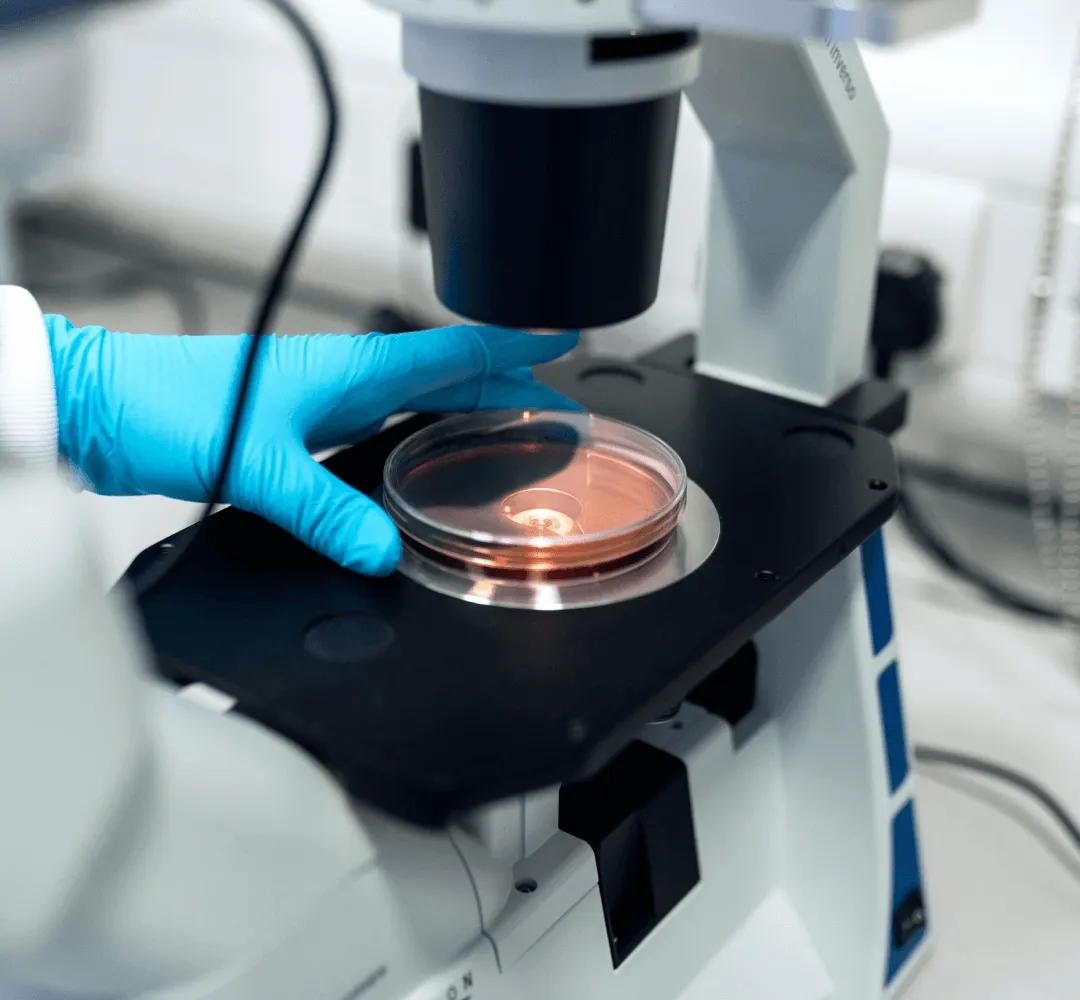
Allozymes is not just about efficiency, it's about reimagining entire industries.
product
Phytoene
Take phytoene, a vital ingredient in many products, for example. Traditionally extracted from tomato skins, this process is incredibly resource-intensive, requiring vast amounts of water and land, and contributing significantly to carbon emissions. We offer a sustainable alternative by producing phytoene using engineered enzymes and yeast.
Environmental Impact of Traditional Methods
Producing 1kg of phytoene requires a staggering 16 Olympic-sized swimming pools worth of water for tomato cultivation.
The process emits 760 tonnes of CO2 per kilogram of phytoene produced.
Extensive land is needed for tomato cultivation, contributing to deforestation and habitat loss.
Our Solution
This method eliminates the need for large-scale tomato cultivation and its associated water usage.
Significantly less CO2 is released compared to traditional extraction.
Allozymes uses 24x less solvent than traditional extraction methods.
The process allows for scalable and controlled production of phytoene without relying on resource-intensive agriculture.
product
Bisabolol
Similarly, the extraction of bisabolol, a compound prized for its skincare benefits, has historically relied on harvesting Candeia trees, a practice that threatens rainforest ecosystems.
Environmental Impact of Traditional Methods
Harvesting of Candeia trees or German chamomile for bisabolol extraction contributes to deforestation and biodiversity loss.
89% of the Atlantic rainforest, home to the endangered Candeia trees, has been lost due to unsustainable practices like bisabolol extraction.
Producing 100 tonnes of bisabolol requires harvesting Candeia trees from an area larger than the entire country of Singapore.
Endangering the Candeia tree species and disrupting the rainforest ecosystem.
Our Solution
Engineering a custom enzyme to biomanufacture bisabolol eliminates the need for harvesting trees and preserves natural resources.
Biomanufacturing protects the remaining rainforest and its biodiversity.
Eliminates the need for vast land areas dedicated to Candeia tree or German chamomile cultivation.
Provides a nature-identical alternative to naturally sourced bisabolol.
Allows for controlled and scalable production to meet the growing demand for bisabolol sustainably.
UN Sustainable Development Goals
- 2
Zero Hunger
- 6
Clean Water and sanitation
- 9
Industry, innovation and infrastructure
- 12
Responsible consumption and production
- 15
Life on land